More than any time in recent memory, the global community has united in the pursuit of a common goal: to develop a COVID vaccine that allows for the return of normal life. While COVID has had a significant impact on the Butler® business, with record levels of construction activity aimed at bolstering domestic supply chains and e-commerce distribution networks; it may surprise some to learn that Butler solutions are at the center of an evolution in the way pharmaceutical companies approach construction.
The need to rapidly expand capacity in pharmaceutical production was a concern for most manufacturers prior to COVID. Speed-to-market is key to their mission of bringing life-saving medicine to the world’s population and capitalizing on a new drug’s profitability during the patent period. The profits are essential to funding future research and development. The impact of COVID, and pressure placed on these companies to produce enough vaccine for the world’s entire population, has only added to these demands.
As a result, leading pharmaceutical companies have asked their construction teams to move beyond their traditional role as a simple cost-center and embrace a role as a strategic partner in the business. Those organizations are driving collaborative/lean construction models, such as design-build and integrated project delivery, and Butler is playing a key role as a partner on these projects from the earliest phases of pre-construction through the commissioning of these structures.
As is typical with many highly complex projects, pharmaceutical production facility construction usually begins with a stage-gate process, often called Front-End Loading (or FEL). The first FEL stage begins with the selection of engineering and design partners, preliminary design work, and budgeting. With each subsequent phase, a company’s requirements for the building are further defined, and budgets are updated and approved. At the end of this process, the project is fully designed and ready to move into construction.
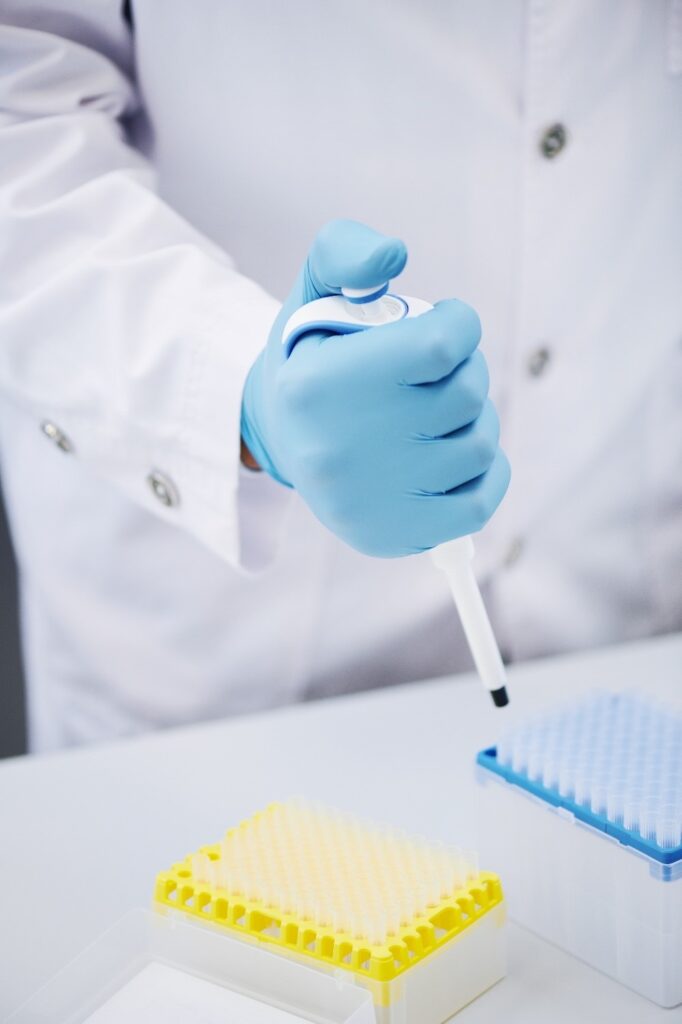
Where Butler Comes In
The Butler engineering and estimating teams start their work with building owners and their engineering consultants, at the end of the first phase of Front-End Loading (FEL 1), with a Butler Builder® engaged around the same time. Butler’s ability to design pre-engineered, conventional, and hybrid structures, and develop budgets around alternative process layouts, allows the owner to make informed decisions as they refine the project’s design across FEL 2 and 3. Anchor bolt layouts and reactions, along with permit drawings, are available at the end of FEL 3. Since the owner has already committed to a Butler building, design teams can move directly into production, detailing, and fabrication, resulting in steel delivery within weeks, if not months, ahead of a typical engagement.
The Butler Builder’s role is where the rubber meets the road, as they are responsible for feedback to Butler Manufacturing on the constructability of design, project sequencing, and construction coordination with the other trades that the owner involves in the collaborative design process. Butler and the Butler Builder work together to facilitate lean construction strategies of Takt time planning, just-in-time delivery of materials, and off-site/modular construction. These methods significantly compress traditional construction schedules while substantially improving job-site safety and productivity.
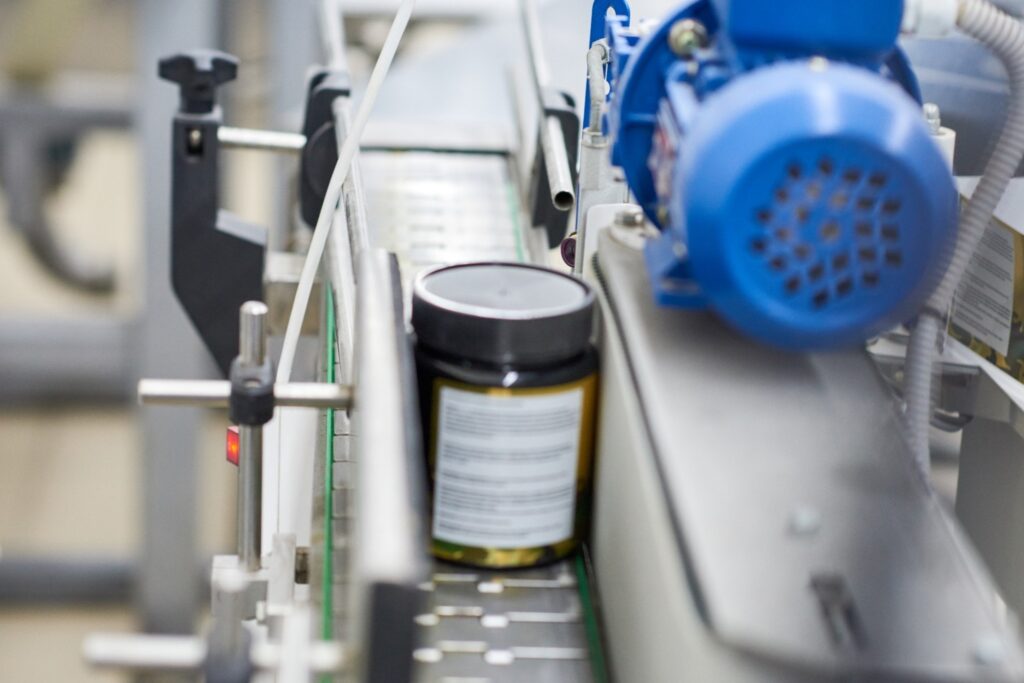
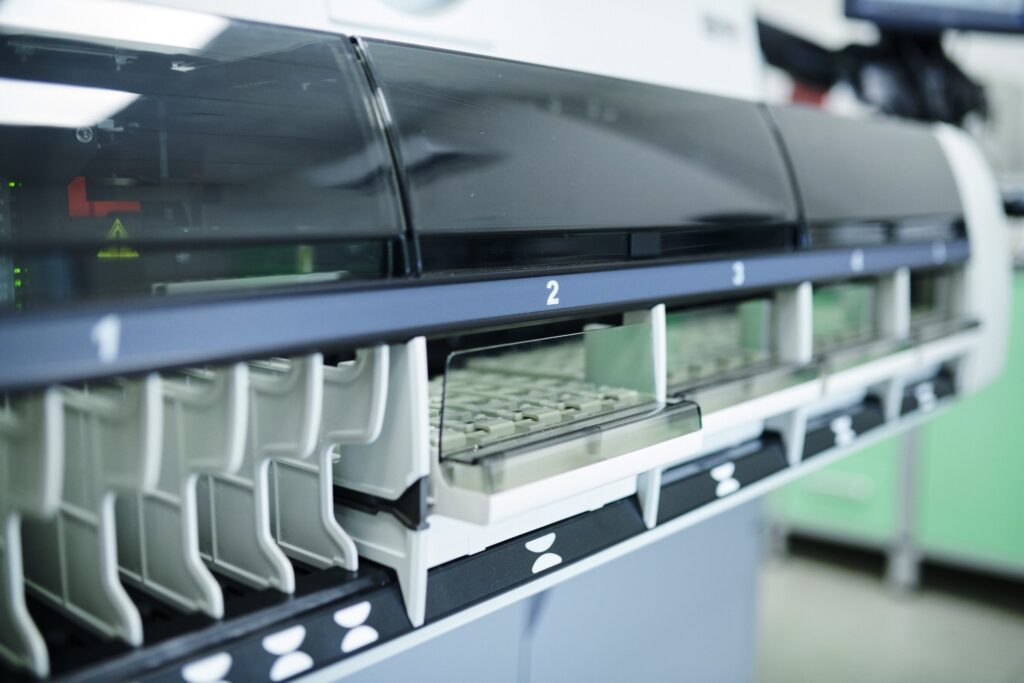
Tangible Results
Along with making life-saving medicines available to the public faster and less expensively, these collaborative/lean construction strategies yield significant, tangible business results by reducing overall schedules by six to eight months relative to a standard design/bid/build engagement. Compression of the project delivery schedule, including pre-construction and construction, leads to lower administrative costs and reduced costs for general conditions. Additionally, when considering the number of doses produced in a month, and the income generated from those doses, the net benefit far exceeds any savings an owner could hope to gain through a design/bid/build process, which would have added months to the 24 week delivery of the first building.
In an effort to further the progression of lean construction on pharmaceutical projects through collaboration, Butler teams up with the Engineering, Procurement, Construction Management and Validation (EPCMV) firm, Integrated Project Services (IPS), modular clean room manufacturer G-CON, and Butler Builder SPAN Construction, on IPS’s ICON building product. The ICON product takes off-site and modular construction to the next level, as IPS designs pre-engineered production processes that can be contained within G-CON’s cleanroom pods.
Pod construction, and installation of the process within them (including all MEP’s and finishes), takes place in and off-site controlled environment, and in parallel with the construction of Butler buildings designed to contain the pods. When the building is ready to receive the pods, they are shipped to the construction site, and rolled into the completed Butler Building for installation. By moving from a linear construction sequence, to a parallel approach, ICON projects will take 15-18 months to go from concept to production, making it a true disrupting approach to pharmaceutical facility construction.
Along with changing the paradigm on project delivery speed, the ICON product offers future end-use flexibility to manufacturers that are unattainable on buildings using stick-built clean rooms and interstitial MEP spaces. Taking a modular approach, the owner could repurpose the building, with very little change to the Butler structure, by swapping out one set of process modules for another. Given the durability of Butler buildings, and the patent window for pharmaceutical products, it is conceivable that ICON buildings could house 2 or 3 different manufacturing processes during the lifespan of the structure.
A Pre-Engineered Solution
While conventional wisdom would suggest that “pre-engineered” buildings are not an ideal fit for pharmaceutical manufacturing, these examples point to how Butler solutions have evolved over the last 20 years. Rather than focusing on a specific structural system (3-plate vs. mill steel), or type of cladding (single skin, insulated metal panels or hard wall; MR-24 or deck/membrane roof), the flexibility afforded by the Butler Conventional Steel Services group allows us to bring the advantages of our systems-construction methodology (design efficiency, erection speed) to any type of project, allowing the building to be what it needs to be, rather than forcing it into a rigidly defined design.
Capitalizing on this design flexibility, owners have engaged with Butler on over a dozen PEMB, conventional or hybrid pharmaceutical sector projects in recent years, and the first two ICON buildings are currently in the early stages of design. As more owners challenge their project delivery teams to deliver building faster, safer, and more cost effectively, we expect to see more of them looking for alternatives to their traditional design, bid, build formula. By working with our Butler Builders, and other alliances partners across the industry, Butler stands ready as a valuable resource for these teams moving forward.
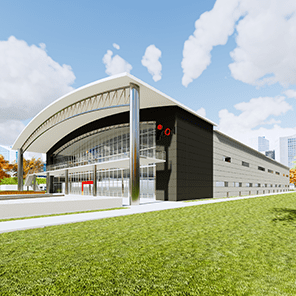