As early as Q1 of 2020, before the pandemic became a major economic factor, logistics real estate was enjoying historically low vacancy rates, as low as 4.5%. Due to this lack of available space, many business owners were preparing for the construction of new and expanded facilities. When shelter-in-place orders rolled-out across the U.S., some industries slowed down. However, demand for logistics-related facilities, including warehouses and distribution centers soared.
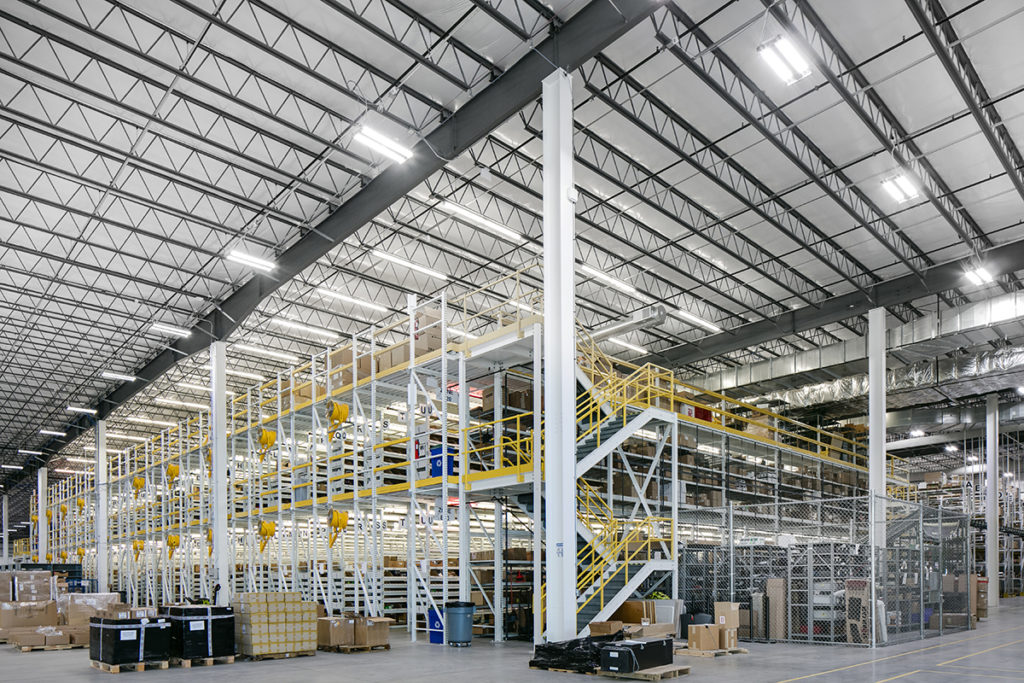
Driving Demand
According to Logistics Management, three key factors are driving the need for and development of warehouse and distribution centers. They include e-commerce, reverse logistics (returned merchandise), and increased inventory necessary to support business operations. In support of this demand, Logistics Management identified a change in consumer shopping behavior, such as customers who may not have previously shopped online needing to make purchases online in response to the pandemic. For example, seniors, considered a higher risk for contracting the virus, made a considerable shift to online shopping. Shoppers using online channels shopped for groceries, medication, home goods, exercise equipment, and boredom-busting activities, like puzzles and board games.
The shelter-in-place-orders coupled with changing consumer behavior directly benefited retailers who saw revenue increases as a result. For Q1 of 2020, Amazon reported a 27% increase in revenue, while Walmart reported an increase of 74% for online sales and Target reported an increase of 141% for its online sales.
Supporting Explosive Growth
- Single source responsibility
- Independent construction professionals who undergo comprehensive training from Butler
- Collaborative, custom designs ideal for your business requirements
- Lower, in-place construction costs
- Industry-leading innovation and technology
- Tested assemblies to meet the most stringent energy codes
- Integrated manufacturing capabilities
- Butler Express Mezz™ freestanding mezzanines
Essential for Excellence
Butler Manufacturing has several products in its portfolio designed to position your warehouse or distribution center for excellence.
The Butler MR-24® roof system provides long-lasting weathertightness for your facility. For more than 50 years, it has been a go-to choice for industrial and commercial builders across the country. Specifically designed to accommodate roof movement under changing temperatures and with a UL Class 90 wind uplift rating (approved by Miami-Dade County), this is THE roof to protect your valuable inventory and the workforce who keeps it moving.
The Landmark™ 2000 structural system combines solid-web primary frames, Truss PurlinXT™ secondary structural members, and rod bracing to allow for 60’ of clear space between columns. Truss PurlinXT is ideal for buildings requiring clear, open interior space for equipment placement, racking, and storage.
The Butler Express Mezz™ System is a freestanding mezzanine system that can support light loads for office space or heavy loads for storage. No welding is required for installation, making this an easy way to get more of the flexibility out of your building and its features.
Beyond the Warehouse
Explosive growth in e-commerce is influencing business needs beyond the physical space necessary for operations. There is a growing need for data centers to process and store consumer data, including payment information, purchase history, and additional data points that support e-commerce. According to Grand View Research, the global data center construction market is expected to grow at a compound annual growth rate of 8.5% between now and 2027. In direct response to the pandemic, shifting consumer habits, and an increase in telecommuting, Technavio predicts the CAGR for the data center market could be higher than 10%!
Details Matter
Butler has built more than 2 million square feet of the most advanced hyperscale data center ecosystems in the world. Butler has experience designing, engineering, and manufacturing projects, including co-location, cloud, and enterprise facilities. Butler knows the details matter – climate control, a redundant roof, and other elements are essential to protecting your business-critical data.
The Butler Difference
A Butler building system offers flexibility to support warehousing and distribution operations, as well as data center needs. You can design and build for size, growth, or future innovations. Building owners can incorporate cranes for inventory management, smart warehouse functionality, employee amenities for workforce retention, or office space.